UN Chose Neoloy to Stabilize Ground for Air-based Aid
The Neoloy Tough-Cell airstrip rehabilitation provides a stable base for aid operations in an impoverished region, facilitating delivery to millions of people in food crisis and literally helping the UN save lives.
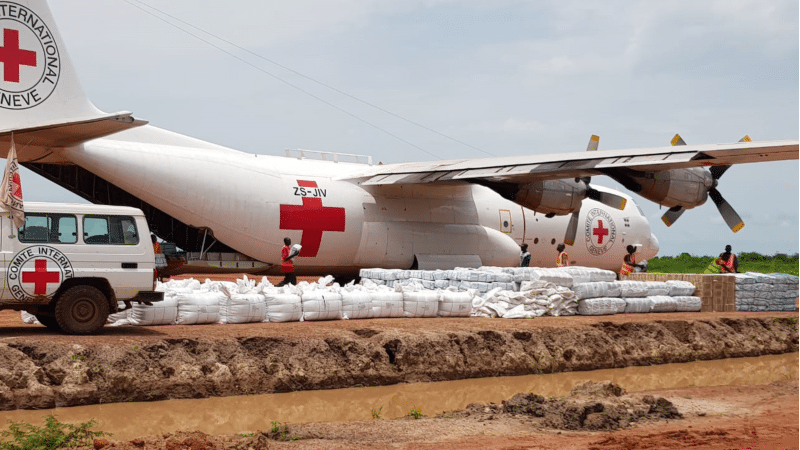
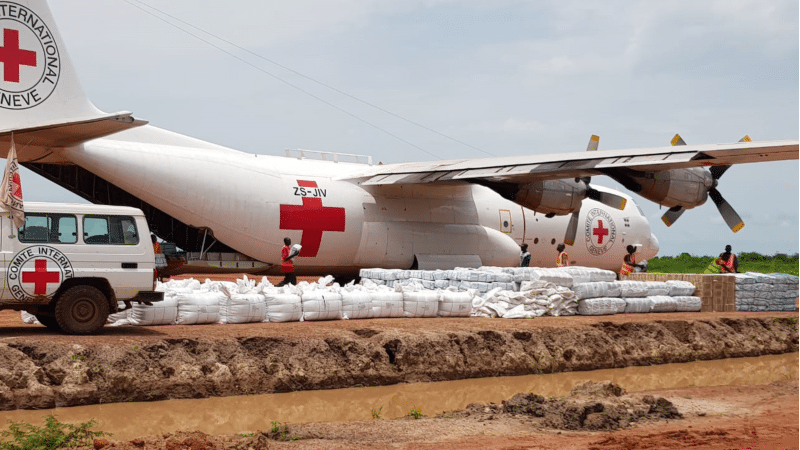
Challenge
UNOPS (United Nations Office of Project Services) needed to rehabilitate the Rubkona airfield: taxiway, apron and access roads (including drainage) as well as double the runway size to accommodate larger aircraft (e.g., C130 Hercules). This was a lifesaving mission to guarantee steady airborne deliveries of essential aid to millions of people vulnerable to insecurity, displacement, food shortages and disease.
Neoloy Solution & Benefits
In a competitive international tender the UN chose the PRS solution. The PRS Engineering detailed pavement analysis and design was a critical factor in their UN decision. The report proved how Neoloy Tough-Cells were the optimized solution for the project conditions:
- Local sandy soil used as the primary pavement material
- Tough-Cell with proven geocell stable geometry for the entire design life
- 40% reduction of pavement thickness
- Low maintenance – only routine surface leveling
The airfield design consists of a formation level and in-situ material roadbed. The Neoloy Tough-Cell were installed over the entire area of the airfield with significant overfill. The airstrip was basically constructed from sand, with somewhat higher quality imported Murram sandy-gravel infill limited to the wearing course.
Why Neoloy
The optimized solution required for reliable heavy-duty use was based on the following geocell engineering parameters:
- High elastic stiffness – to withstand dynamic loading from moving aircraft and vehicles over time
- Low permanent deformation (creep) – to ensure that geocell reinforcement is maintained for design life
- High tensile strength – to withstand heavy stresses from aircraft and vehicles
The high reinforcement factor of Neoloy Tough-Cells optimized the design of the airfield. Local soil was used for structural infill, while minimizing the need for imported gravel. This not only reduced construction time, it also made the project very cost-effective, sustainable and low maintenance.
In terms of manufacturing and logistics, PRS was able to deliver the entire quantity of several hundred thousand sqm within 10 weeks to Mombasa Port to meet the UN’s urgent needs.